ATEX PSI Equipment includes the following items :
Sensors ITM ATEX
ITM Technologies detection sensors offer exceptional performance. They make possible the detection of the smallest leaks which are invisible from the naked eye, and thereby prevent any undesirable pollution. Furthermore, the sensors are automatically identified when the connection is established. ITM Technologies sensors have a cable length between 10 and 20 meters. They can be immersed in a wide range of chemical products and are ATEX certified for applications in explosive areas.
Gas filtration before discharge
Sensors ITM ATEX
It’s mandatory to filtrate gases before rejection by the vacuum pump when underground tanks tightness tests are done with special liquids (industry) or in specific configurations (underground service stations). The PSI module is equipped with a parallel circuit that can be used to pass gases through an easily replaceable activated carbon filter.
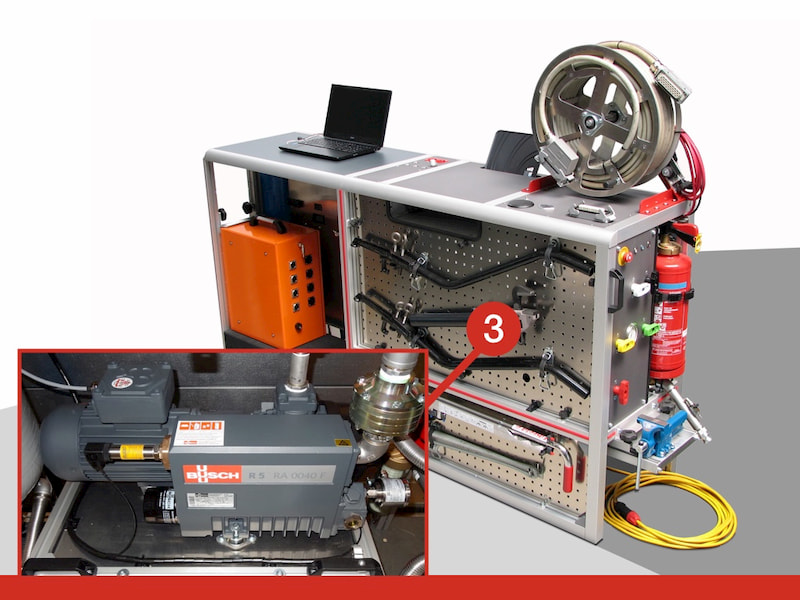
Vacuum pump ATEX
The ATEX vacuum pump is of high reliability and is mounted on a side sliding plate, which makes its maintenance extremely easy. It is coupled to a frequency converter to modulate its flow to be able to adapt to different situations.
Integrated security
Working in explosive atmosphere involves precautions. The gas detector automatically cuts the electrical installation in case of danger. Other safety devices (pressure, temperature) cuts off its power supply if necessary.
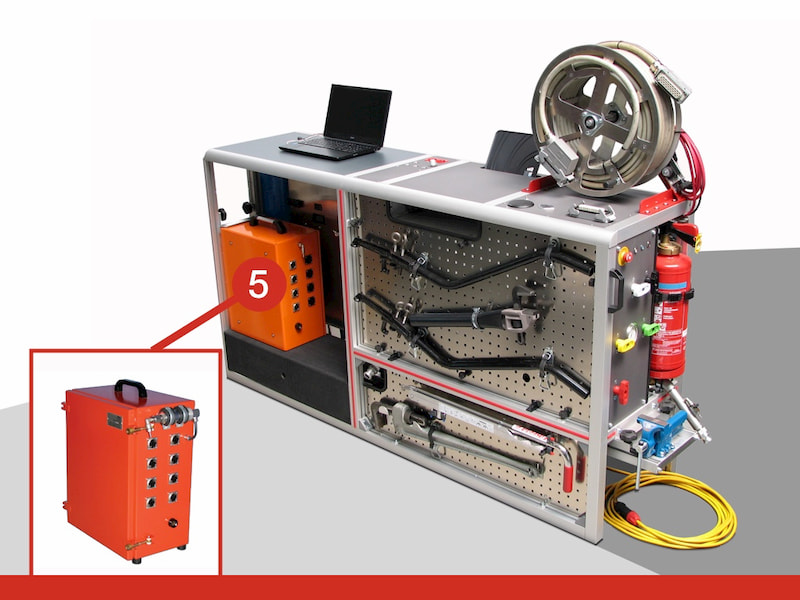
Toda-Unit
It transmits data from the sensors to the computer. The data acquisition TODA Unit makes connection of up to 40 meters from vehicle to tank and simultaneously enables the testing of 4 tanks.
Computerised office
The ergonomic workstation is located inside a vehicle protected from climatic conditions.
Computer-assisted tightness tests allows printing , recording and replay mode. The computer software also makes it possible to control other peripherals (vacuum pump, security, lighting, …).
The PSI module allows you to control:
The tightness of cylindrical horizontal tanks
The tightness of single or double walled tanks (inner wall).
The tightness of empty tanks or tanks containing a fluid product.
The tightness of the pipes associated with the tank.
and, thanks to the specificities of the integrated Toda-P module, it also allows you to control:
The tightness of pipes only and disconnected from the tank.
The tightness of the interstitial space of the double-walled tanks.
The tightness of the interstitial space of the double-walled tanks.
The tightness of any vacuum resistant volume
TODA-15© acoustic method ITM TODA-15
The ITM TODA-15® testing method combines depressurization (vacuum) of tested components (pipes, tanks, accessories) with acoustic detection of “leak noise” in case of tight defects. The depressurization is the dynamical element which generates the emission of turbulences in non-tight areas. The “leak noises” (turbulences) are detected thanks to the right position of the sensors in the controlled Underground Storage Installation (Pipes, tanks (UST). The ATEX sensors are connected to the electronic interface TODA Unit. It enables the acoustic signals processing, the tightness testing and monitoring. The ITM TODA-15® testing method is mainly used in Storage Installation working under atmospheric pressure.
Advantages of ITM ATEX equipments :
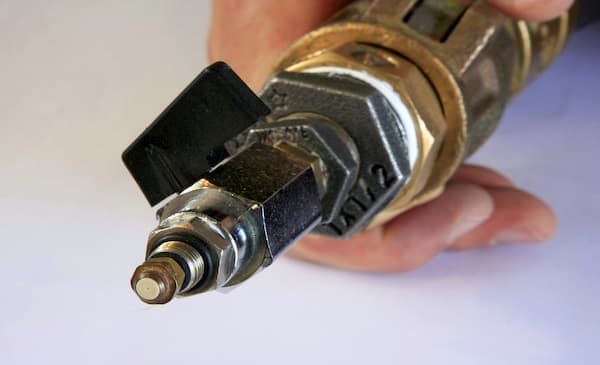
Highly-appreciated accuracy
The TODA-15 © acoustic method detects leaks of 15/100 mm located on piping far from 25 m to the sensor (located in the tank), identify the problematic equipment, and most of the time locate it very precisely.
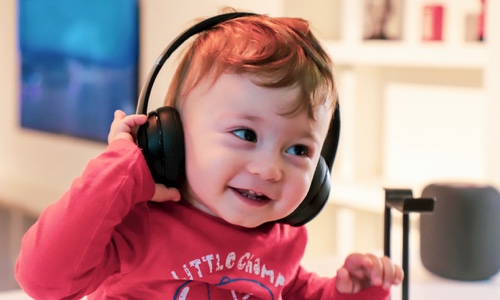
Intuitive listening
The excellent sound quality can be hear from integrated speakers to ensure greater freedom of movement on the worksite.
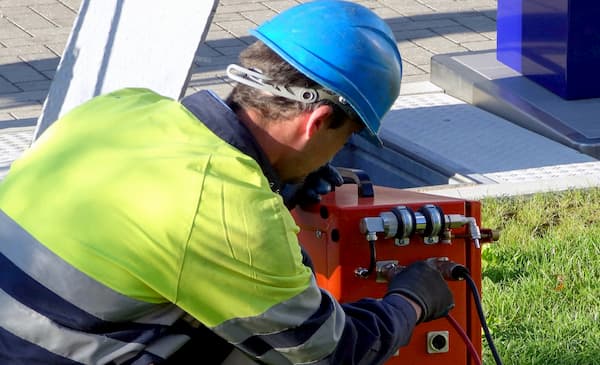
Efficient tests
Tank and associated piping tested simultaneously.
No need to disconnect the pipes from the tank.
Tests made with the fuel contained in the tank (10% to 90%).
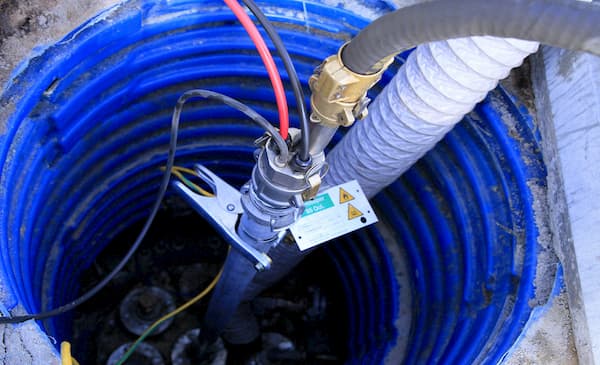
Reduced dismantling operation
It’s very important to keep the tanks and pipes connected during the test. Don’t dismantle pipes from tanks during tests otherwise you may create a leak that didn’t exist before or miss a leak that exists before the test.
TODA-15 equipment meets this criterion :
Tank and associated piping tested simultaneously.
No need to disconnect the pipes from the tank.
When several tanks are interconnected (by suction pipes, by recovery vapors, …) without the possibility of dismantling, the ITM equipment makes it possible to test up to 4 tanks and associated pipes simultaneously.

Computerized management
Automatic management of deadline verifications
Traceability and complete replay mode of the test.
Flexibility and multifunctionality of a computer.
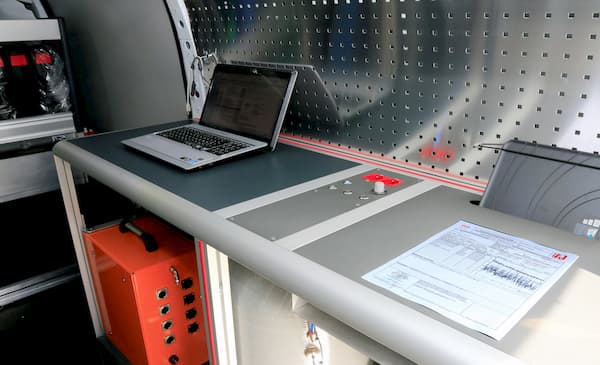
Accurate and immediate reports
- Final technical certificate issued at the end of the inspection.
- Certificate meeting the ISO/IEC 17020 (No. 322-INSP) criteria.
- Software in the language of the user.
- Simplified administrative work.
We are both a specialized inspection body and designer / manufacturer of our own technology. Our tests need to be highly effective that’s why we equip our own response vehicle with a complete installation and supplies dedicated to controls.
- Autonomous work – the vehicle has:
- ATEX PSI module.
- 70 m of markings (stakes and construction net 1 m high).
- All the specific tools (keys, etc.).
- Seals of all kinds.
- Various screws.
- Assortment of fittings.
- Secure scaffolding (workstation up to 5 m to seal vent pipes).
- Ergonomic vehicle.
- Drawers opening towards the outside of the vehicle, limiting the trips in the van.
- Hardware hung on the doors for the same purpose.
- Comfortable office position, away from extreme weather conditions.
- Awning incorporated in the rear doors (deployment in 10 sec) protecting men and equipment.
- Drawer of 180 Kg of load opening laterally outside to facilitate the good postures.
- Reinforced interior and exterior lighting.
- Workstation “workshop” sliding ve (vise, …).
- Arranged and secure for work in ATEX area.
- Extinguisher.
- Built-in gas detector cutting the entire electrical system in case of danger.
- Vapor discharge trough vent pipe incorporated in the vehicle and deployable at 4.5 m height.
- ATEX vacuum pump.
- Vacuum pump cellar ATEX.
- ATEX exhaust fan.
- Tripod, stop fall, recovery winch, …
- Flash lamps.
- A place for each tool, each tool in its place.
- The vehicle remains tidy and offers a beautiful image of the inspection body.
- Enormous pride of the insopector to use an upscale equipement.
- Stowage of all furniture and equipment in accordance with the regulations in case of collision.
- Vehicle risk analysis validated by SGS.
- Validation of the electrical installation by approved organization.
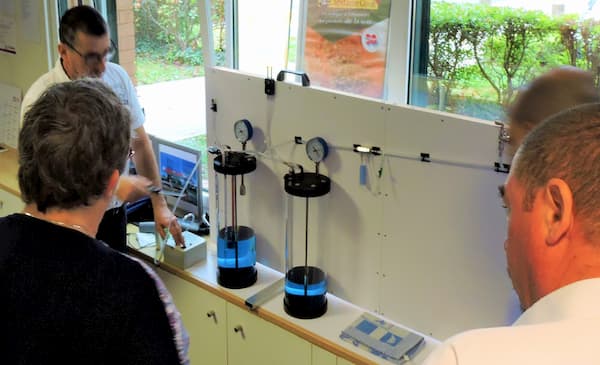
Trainings
Technology without know-how is insufficient. That’s why we offer tailored training for organizations wishing to deepen or acquire knowledge of this very specific profession.
Training related to TODA software: the TODA software is very user-friendly, training is nonetheless integrated; it covers all the features and recommendations to get the most out of it.
Some parts of the PSI module are inseparable from specific learning and procedures, the training program also incorporates this aspect.
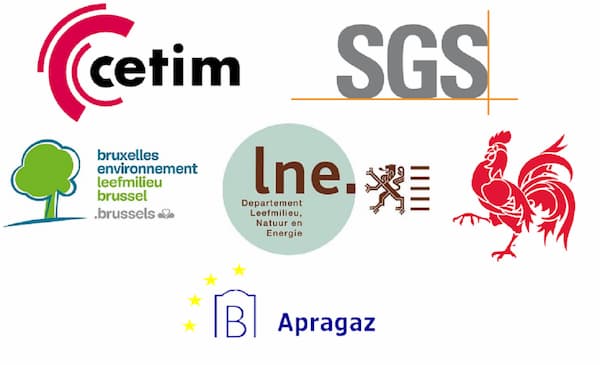
Legal recognition
ITM technology and its evolutions have been tested and approved by several organizations in several countries:
CORCON according to EPA requirements
APRAGAZ
CETIM
SGS
These awards enabled ITM to obtain the necessary approvals from the different ministries to carry out its control missions.
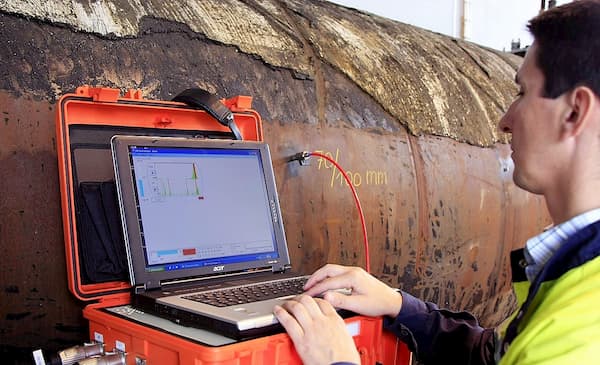
After sales and verification
After Sales Service and verification are provided by ITM – we already provide these services in several countries:
Periodic verification of the sensors and the measuring chain.
Repairs or replacement of elements.
Software updates.
Fast delay.
Our clients are petroleum companies, inspection bodies, industries and dealers..
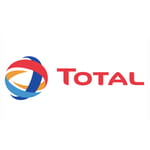
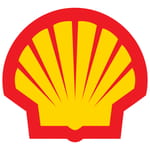
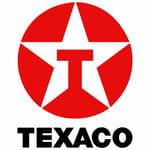
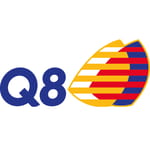
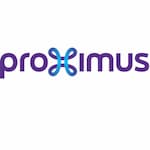
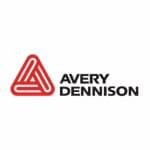
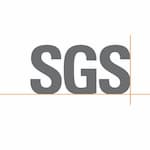
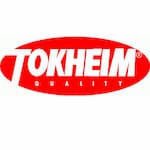
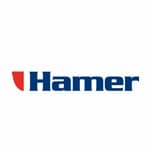
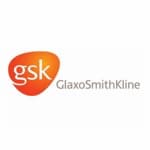
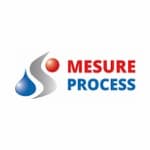
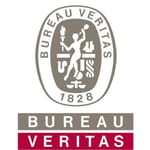
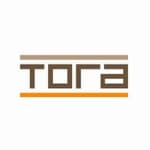
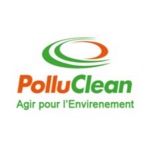
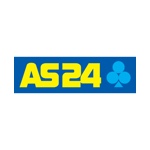
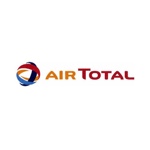
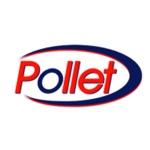
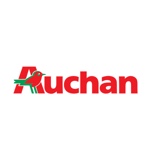
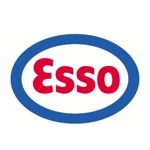
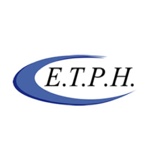
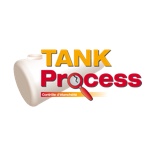